Top 3 Beverage Shipping Challenges & Solutions
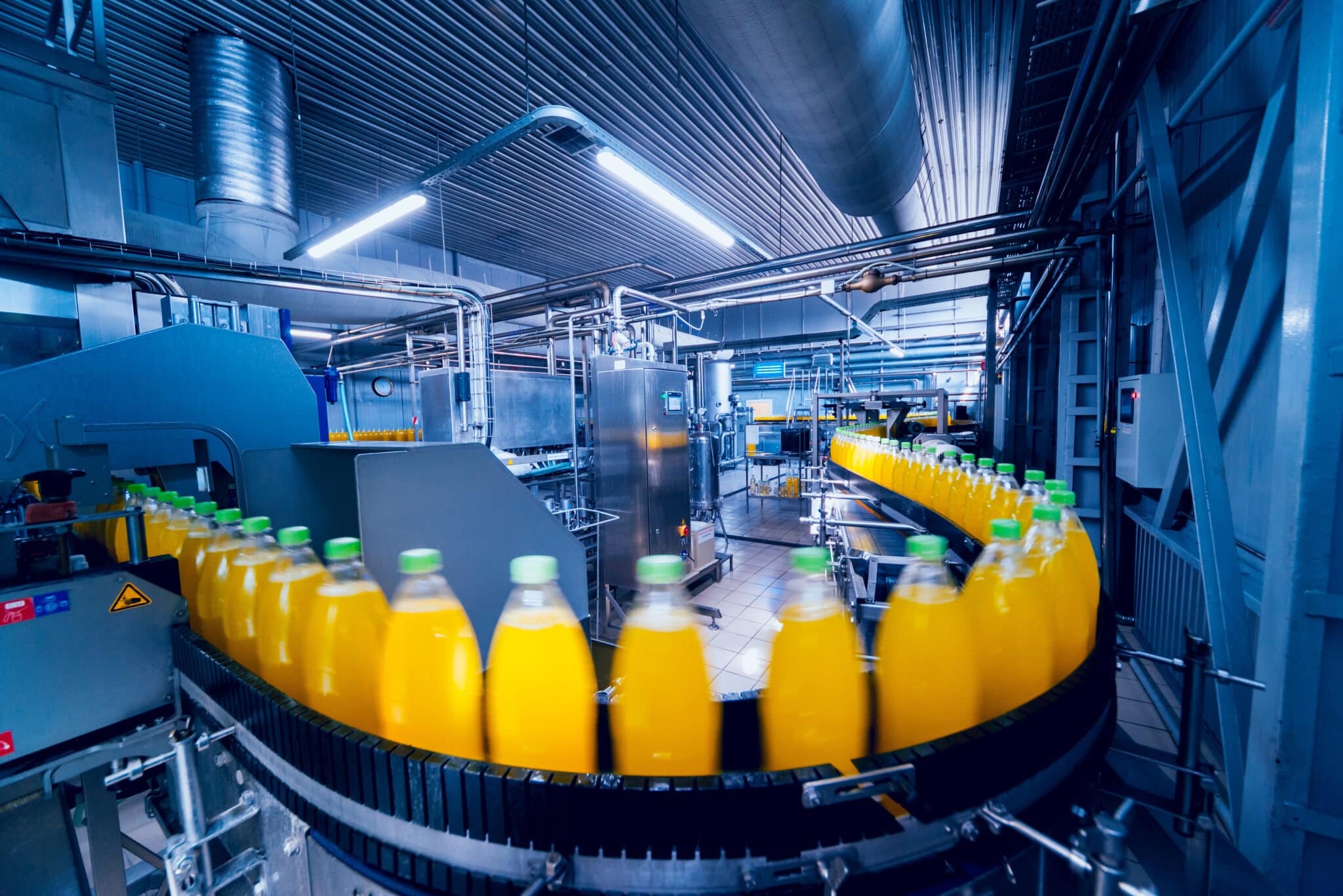
All shipment types come with their own unique set of challenges–and leaders in the beverage industry know this especially well. Moving freight successfully through the beverage supply chain comes down to mastering those specific challenges. Once you understand what you're up against, you can keep shipments moving efficiently, meet delivery deadlines, and maintain quality standards without breaking your budget.
1. Increased demand for traceability
Where is my shipment?
It’s a question you shouldn’t have to ask your freight suppliers. Understanding exactly where your beverage shipment is and what issues may impact its delivery are mission-critical. Beverage manufacturers and sellers should be able to access detailed reports on individual shipment status’ helping to identify potential issues in their supply chain and make better predictions.
People are also paying attention to origins, eco-labels, and other signs that increase visibility and guarantee authenticity of the product. Today’s consumer is more aware of their lifestyle choices, and often consider where their fruit juices & distilled spirits come from. In fact, one survey shows that 83% of consumers say food and beverage companies have an important role to play in food safety. Yet, just 13% felt the industry is currently well prepared to manage food traceability and be transparent about how food travels through the supply chain.
2. Complex communication issues
A beverage supply chain relies on a huge number of partners and suppliers in order to run smoothly. When poor communication leads to late shipments, the results often go deeper than a delay.
A single missed deadline for anything from a key ingredient to raw materials needed for packaging can cause a ripple effect that could take days or even weeks to resolve. For manufacturers outside of the food and beverage industry, this could mean missing timelines or even lead to a product shortage. Perishable goods in certain beverages can’t simply wait on shelves while that delay is addressed. Everything needs to come together just right, and the longer the delay goes on, the bigger the risk.
3. Need for exceptional quality control
Of all the food and beverage supply chain challenges, preventing delays during the beverage transportation process is crucial to deliver a quality product. This is especially important for perishable drinks that require specific and constant temperature controlled transportation. If standards aren’t met or if delays impact timelines, they can easily lead to wasted product and lost revenue.
Of course, while many quality issues are caused by late delivery, other causes can include poor storage conditions, messy warehousing and timely inventory management. Experiencing any of these can result in decreased product quality, and in some of the worst cases, result in food-borne illness. With the majority of recalls costing over $10 million–improving end-to-end shipment monitoring is vital.
How to solve beverage transportation challenges
- Enhance visibility — In order to be able to track and trace the source of a batch of products, or to predict changes in supply and demand of the raw materials used to produce them, you need true end-to-end visibility. Extending visibility, potentially via IoT provider integration, from the source of raw materials through to customer delivery helps you address issues before they arise.
- Understand risks — Every beverage supply chain comes with risks, and understanding them is key to keeping them running smoothly. Predictive analytics powered by AI and machine learning can show you exactly what’s happening–and what’s likely to happen next. By pairing these tools with a supply chain digital twin — a detailed simulation model of your beverage transportation supply chain created using real-time data — leaders can explore various “what-if” scenarios to determine risks and potential impact in order to develop solutions well in advance of any disruption.
- Strengthen flexibility — By extending your capacity network to include more options from multiple modes and carriers, you can severely limit disruptions from carrier capacity shortages. Pairing this with full visibility and intelligent automation brings additional opportunities, automatically suggesting the best way to optimize loads, consolidate routes and maximize every mile.
- Improve communication — Strengthen relationships through quick response times and accurate information on changes to ETAs and other vital details by keeping an open line of communication with all partners, drivers and others involved in your supply chain through a centralized platform..
Keep your beverage shipments flowing with confidence
Beverage shipping requires more than just reacting to challenges - it demands proactive solutions. By enhancing visibility, understanding risks, strengthening flexibility, and improving communication, you can ensure smooth operations, maintain product integrity, and keep your supply chain moving efficiently.
With Shipwell, you gain the technology and support needed to optimize every shipment, reduce disruptions, and deliver quality products on time, every time. Stay ahead of demand, minimize risk, and take control of your beverage supply chain. Request a demo today.