Rising Fuel Prices Push Shippers Toward Efficiency
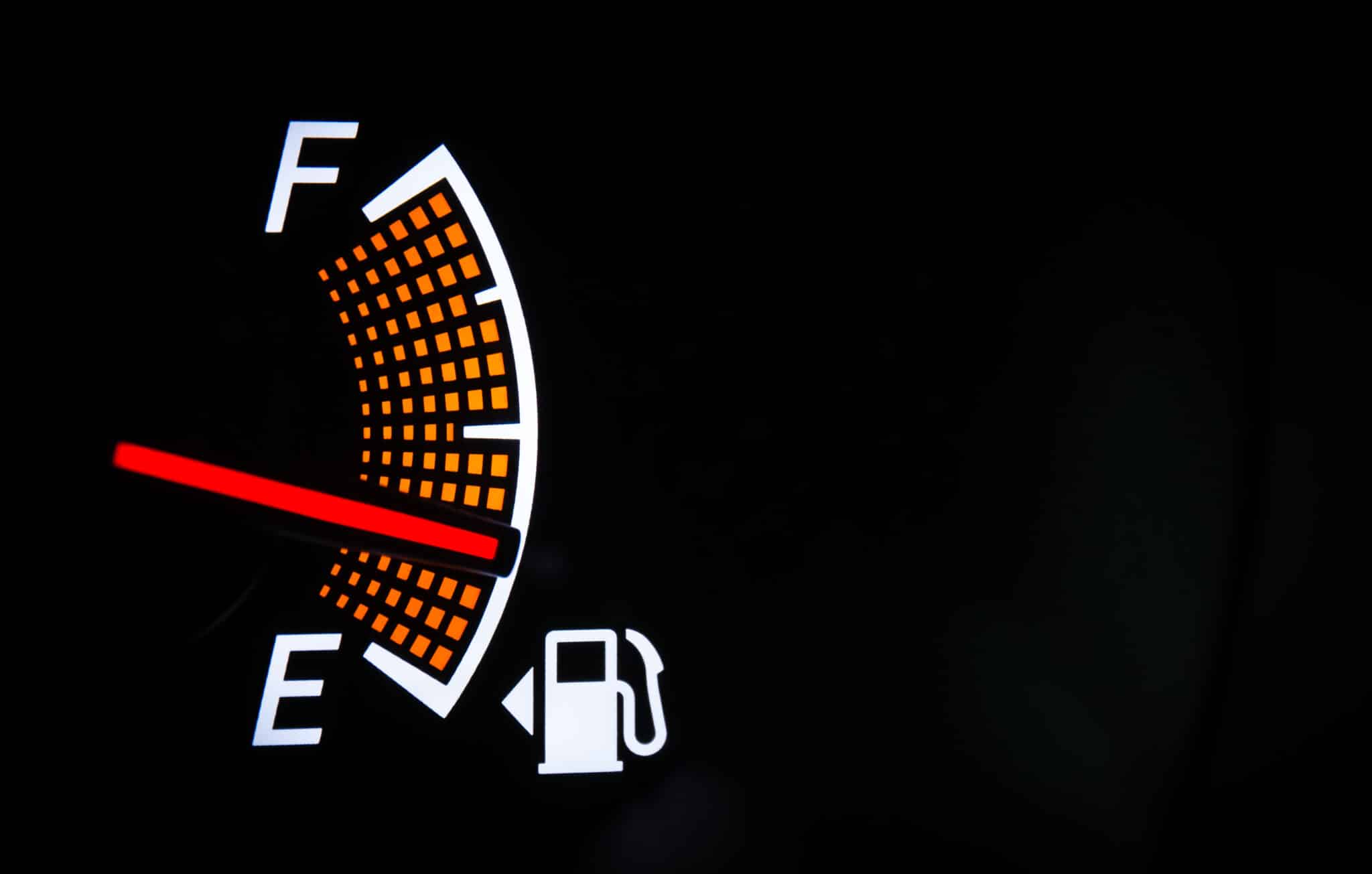
On Wednesday last week, the average cost for a gallon of regular gas in Los Angeles reached $6.08 according to the latest data from AAA, leaping 2.3 cents overnight and breaking a record set earlier this year. At the same time, diesel prices rocketed higher across the country as well with prices hitting an all-time high of $5.577 a gallon, up 76% over the past year. And with average gas prices in Los Angeles increasing to $6.098 as of Monday this week while hitting a new high of $4.599 nationally on Wednesday, and the average national diesel price dropping only slightly to $5.544, it's looking like fuel prices have nowhere to go but up.
For those operating supply chains these record-high prices mean an increase in both operational and product costs, so both the business and consumers are affected. And pairing this issue with the ongoing driver shortage, skyrocketing inflation and already elevated freight costs, the price of keeping shipments moving has never been higher.
With fuel prices continuing to rise, companies are faced with the options of operating at a loss, raising prices for their customers, or exploring new methods to save on costs. And with inflation already hitting both businesses and their customers hard, those first two options can only go so far. This has forced many to reassess their shipping strategies and look for opportunities to shave costs and find valuable new efficiencies in their supply chain through improved order consolidation and routing options.
Traditionally, finding ways to optimally consolidate orders into shipments and put them on the most efficient route with the fewest number of trucks required has been a daunting task that, depending on order volume, could take hours or even days out of the week to plan effectively. Packing multiple customer orders into the most ideal mode allows a greater quantity to be dispatched at once, greatly reducing both the costs for the shipper and the number of road miles — and thereby the amount of fuel — needed to get shipments to their destination. But with many performing this optimization via manual process or through third-party software or spreadsheets outside of their Transportation Management System (TMS), uncovering the most efficient options is rarely an easy task.
Assessing each individual order’s size, weight, locations, pickup and delivery times, and consolidating them onto the most cost-effective and available routes and modes is typically a valuable but time-consuming task. However, with automated tools like Shipwell’s Load Optimization, it can now be completed in a matter of seconds.
There may not be much that shippers can do to improve gas prices or inflation, but with improved efficiency, it’s possible to significantly reduce the time it takes to plan and route shipments as well as the costs associated with moving them.
For more information on Shipwell’s new Load Optimization capabilities, click here. Or to speak to an expert about how Shipwell can help you to uncover greater efficiency in your supply chain, schedule a demo today.