How Quality Control Tech Improves F&B Shipping
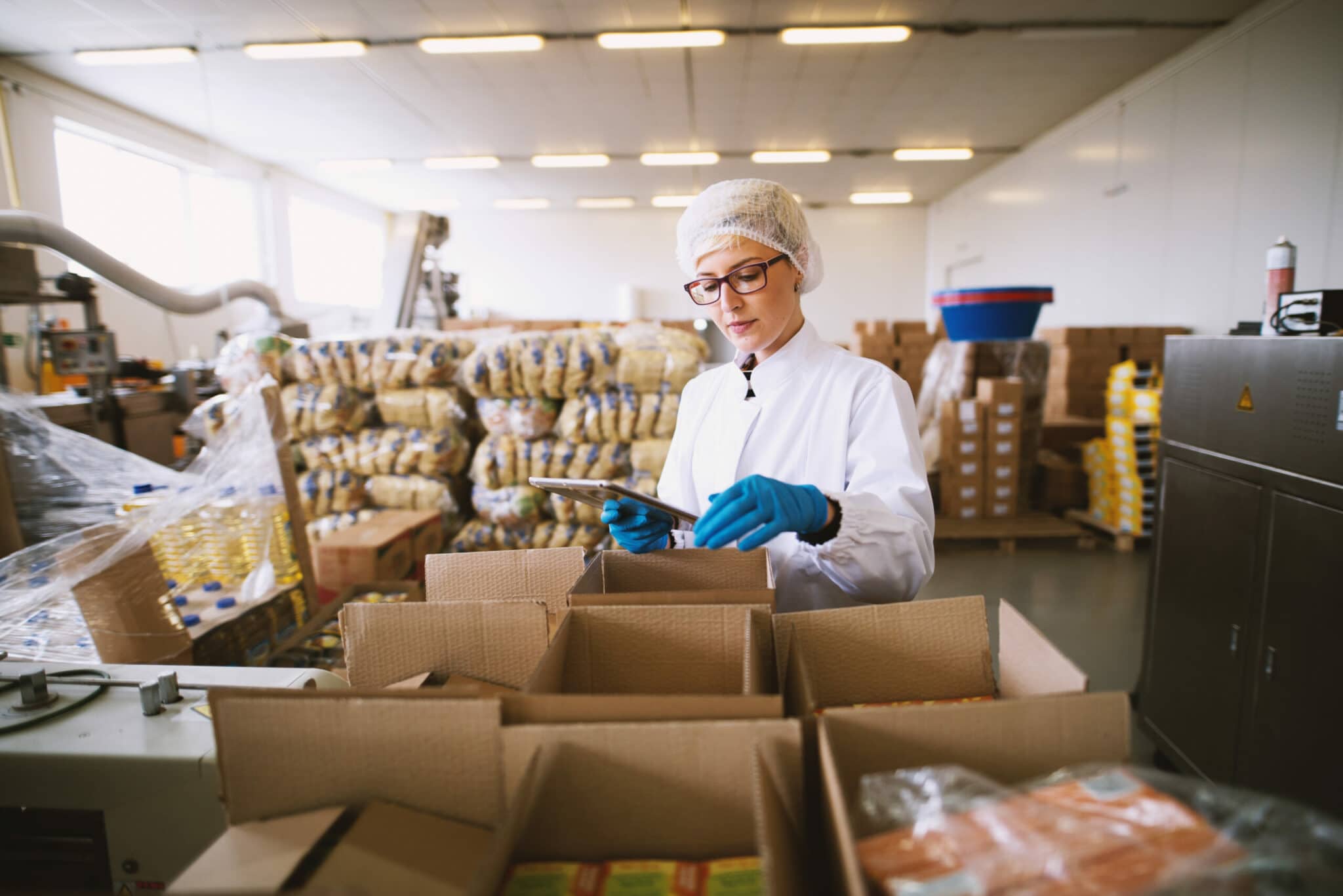
Boost on-time pickup and delivery and respond quickly to serious incidents
This is the third of a three-part series on how companies in the food and beverage industry can transform their supply-chain operations.
Imagine you’re a meal-kit home delivery company. You’ve got all your systems in place to take orders, process the meals, and deliver them. Things seem to be humming along until one of your locations is hit by a hurricane.
Suddenly, your preferred carriers are shut down, and you have to find new ones locally — and fast. What do you do?
This scenario illustrates why quality controls are critical to success, especially in the food and beverage industry. Sure, it’s great to have these controls in place to catch the small hiccups that occur every day. But the real test of your quality control technology is when things go seriously wrong.
Unfortunately, when it comes to running a food and beverage company, a lot can go wrong. (It’s why the industry is so highly regulated.) Businesses like yours can face fines, product spoilage, and unhappy customers.
With so much at stake, quality control technology is your best defense.
The best TMS offers the most effective quality control technology
So what does effective quality control technology look like? What key things should it offer to leverage data analytics and automation, improve your compliance posture, and help protect already narrow margins?
Let’s go over some of the most important quality controls you should make sure are part of your TMS:
- Real-time visibility into shipment status. When integrated with ELD technology, today’s shipping platforms can support real-time status and location updates. This lets shippers automate carrier communications. The right TMS can send emails or make robocalls on your behalf, then use natural language processing to interpret the results, make corresponding updates, and notify stakeholders about what has changed.
- Visibility into carrier performance. A TMS that tracks carrier performance data can provide visibility into on-time pickup and delivery rates, the number of loads the carrier has hauled for the shipper, and how much the carrier is being paid. It can also highlight indirect costs, such as those incurred from late shipments or lumper fees. The right carrier performance data can facilitate faster, more informed decisions about which carriers are able to deliver your meals fresh … and on time. (It really would have come in handy in the hurricane scenario mentioned earlier.)
- Exception management. For food and beverage companies shipping perishables and just-in-time goods, the ability to quickly reroute delayed shipments is critical to keeping goods flowing to their final destination. Don’t wait for your customers to contact you and ask about delayed shipments; identify, mitigate, and resolve exceptions proactively.
- Final-mile control. Integrated parcel delivery provides the visibility, responsiveness, and quality controls that help food and beverage companies in the home delivery and meal-kit space quickly adapt to unpredictable surges in e-commerce demand.
Quality control technology can protect your business through small and big incidents, assuring that your supply chain is resilient, even as your business scales. By reducing costs and improving on-time pickup and delivery rates, you’ll boost your brand’s reputation with customers and partners.
An essential part of an effective TMS solution
Shipwell understands the unique challenges facing today’s food and beverage companies — as well as the challenges you’ll face tomorrow. We help offset industry-wide margin pressures by providing an affordable, cloud-based solution that reduces friction and waste. Our connected shipping platform combines the key ingredients you need to maximize efficiencies and reduce total cost of ownership: the features and functionality of a TMS, advanced visibility, and an integrated partner network.
Download our free white paper, “Shipping for Food & Beverage Companies: A Recipe for Success.”
Check out our other blog posts on the food and beverage industry:
Data analytics in the food and beverage supply chain
Streamline your food and beverage supply chain with data-driven automation